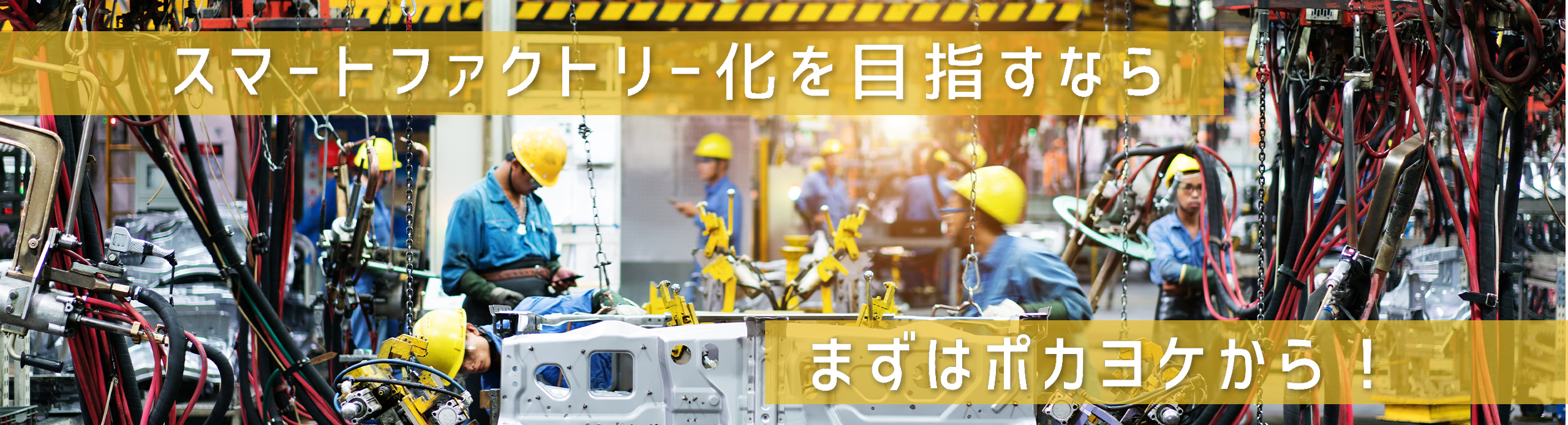
ポカヨケシステム
製造業や物流業における不良品・欠品の原因は作業者(ヒューマンエラー)が大半を占めるとされます。
弊社では30年以上にわたり、自動車業界をはじめとする数多くの製造業や物流業へポカヨケシステムを納入してきました。培われた豊富なノウハウを基に、ご要望のヒアリングから提案まで、お客様それぞれに合ったポカヨケシステムをご提供します。
ポカヨケシステムに関するお問合せ・ダウンロードはこちら
ポカヨケシステムとは?
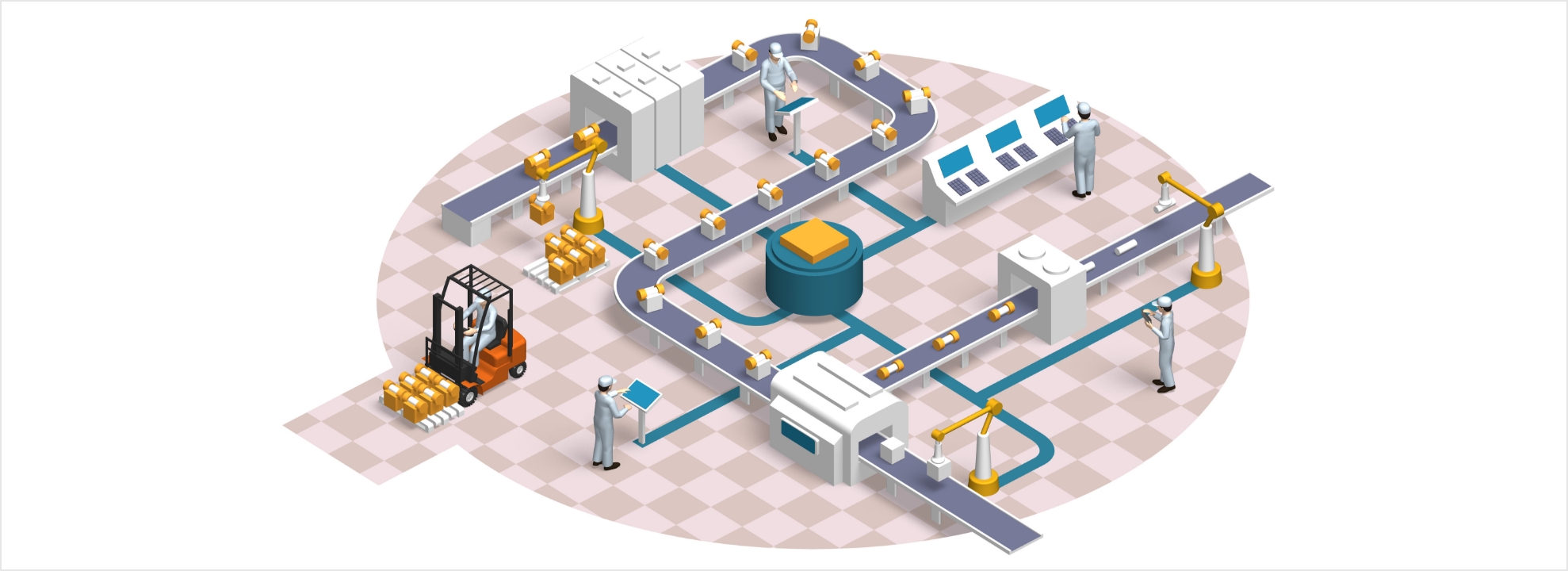
ポカヨケの種類は次のような種類に区分されます。
①検知方法別 ⇒ 識別式(色分け・ICタグ・画像認識)、アラーム式(警報機・センサ)、治具式(ガイドピン・ストッパー)
②目的別 ⇒ 規制式(異常が発生した場合に機械を停止)、注意式(異常が発生した場合に作業者へ注意喚起)
③時系列別 ⇒ 事前(ミスが発生する前の対策)、発生時(ミスの発生時にポカヨケ)、事後(ミスの発生後にポカヨケ)
お客様の困りごとをヒアリングから一緒に考え、最適なポカヨケシステムを提案致します。
ハード・ソフト両面をトータルでご提案
PC系・組込系・PLC系など幅広いソフトウェア技術のノウハウと、
自社で持つ制御工場(制御盤・BOXの設計及び製造)・電子工場(基板設計及び製造)を組合せてトータルサポートのご提案が可能です。 また、ご要望に合わせてSTEPを分けてのシステム導入も可能です。
【STEP1】
ピッキングセンサ・工具などのフィールドレベル(現場側)のみで
ポカヨケを導入し物理的なヒューマンエラーを抑制する。
【STEP2】
事務所にサーバー・PCなどを設置し現場作業データの、
収集・蓄積・分析・予測をしてトレーサビリティ及び品質向上をする。
※ネットワーク構築、各種機器選定からご相談を承ります。

新規導入だけでなく、既設システムの改造・活用も承ります!
新規でポカヨケシステムの導入検討されているお客様はもちろん、
何かしらのシステムを既に導入されており、そのシステムと
連動させて新たなシステムを構築する事も可能です。
【例】
既にピッキングシステムを導入しており、部品投入時に投入する棚はランプ点灯でわかるが、誤って別の棚に投入する事はできてしまう。
⇒各棚へストッパーやシャッターなどを取付けて投入する棚のみ、
開くようにして物理的に投入できないようにする。
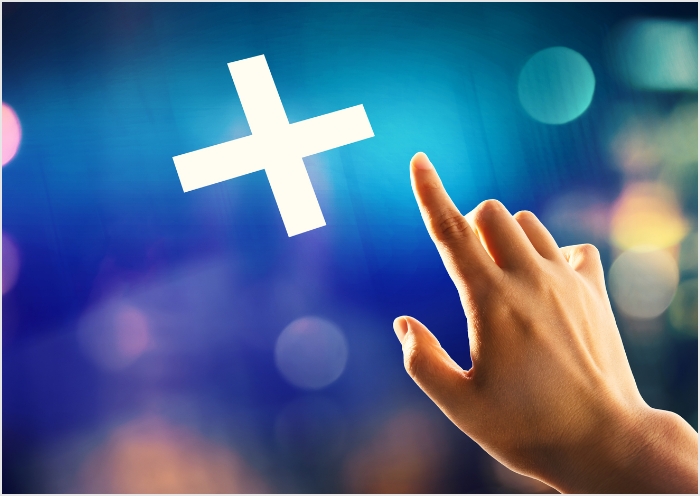
用途・アプリ
1在庫管理システム
荷受場で、部品をバーコードリーダーなどの端末を用いてバーコードを読み取り、入荷データとして在庫処理をPCで行います。
PCには部品棚情報を設定しておき、各棚に対応するラベルを貼付けてあれば、出庫時にバーコードを読み取れば対応した部品が出庫できます。
また、部品発注情報や生産計画などとリンクさせる構築も可能です。
端末や棚に貼りつけるラベルなどはご要望に応じご対応可能です。
端末例:ハンディターミナル(BCR/QR/RFID,有線/無線)
ウェアラブルスキャナ
ラベル例:バーコード/RFID/OCR
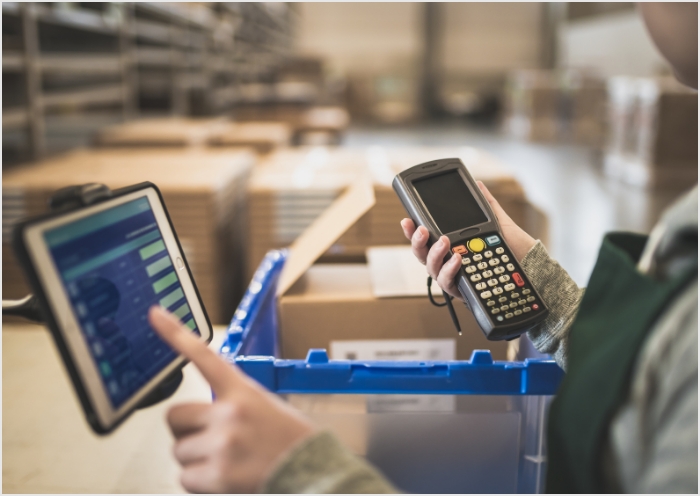
2ピッキングシステム
生産ラインなどで使用する部品を取出す際に、該当する棚を作業者へ指示出しを行います。
指示方法としては、棚ランプやプロジェクターを使用した方法などがございます。
また、ピッキングにプラスしてAGV(無人搬送車)・AMR(自立走行搬送ロボット)・エレカ・台車などの運搬指示/運行管理の構築も可能です。

3作業指示システム
生産情報を元に、PCで集中管理して生産ラインへ部品投入する
タイミングを作業者へ指示出しを行います。
作業者はタブレットなどの操作端末でリアルタイムに情報を
授受して、部品投入後はタブレットで完了操作する事で次の投入指示がPCより送信されます。
現場側での作業者操作は不要で状況だけ見られればよい場合は、
大型モニターを置きアンドンとする事も可能です。
また、部品投入1サイクルの作業実績を収集し標準作業時間との
比較も可能なため、作業改善のツールとしても効果が得られます。
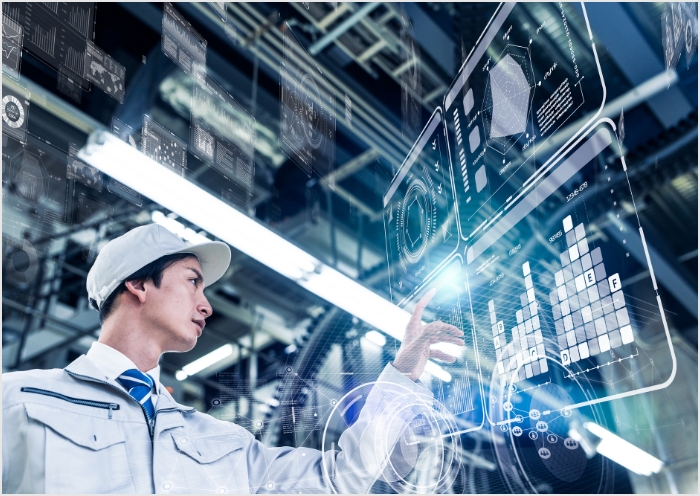
CASE STUDY 採用事例集
-
続きを読む
-